Controlling Color Masonry Mortar
By Jeff Leonard
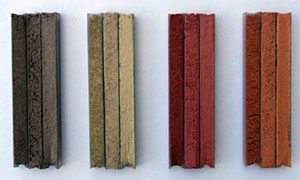
Many variables come together to produce high-quality masonry. Mortar is one of the only job site materials made by hand and as needed. Whether the mortar is made by breaking bags of cement and lime in the mixer and adding sand by the shovel, or using pre-blended materials in 80-pound bags or in 3,000-pound bulk bags through a dispensing system, the importance of achieving the desired mortar color and aesthetic cannot be forgotten. After all, the mortar is the "framework" of the masonry unit.
Take a moment to look at the four groupings of colored mortar channels pictured above. How many colors do you see? Although there are 12 total channels, there are only four different colors. Each of the four sets of mortar channels represents one color. Each of the color sets meets the fundamental requirements to maintain color uniformity. They are:
- Sand from the same source
- The same cement/lime or prepared masonry cement
- The same pigment and a uniform measurement from batch to batch
Furthermore, the color sets represented are each formulated with the same amount of sand, cement and pigment. As evidenced, this alone does not ensure uniformity in color. These samples demonstrate that water demand and striking times matter.
Water demand will vary due to daily weather conditions. Cool mornings require a mortar that is a little stiffer. As a warm day develops, water demand will increase. For these reasons, a prescribed amount of water cannot be necessarily adhered to. Due to varying water requirements, it is important to tool the joints when the mortar is thumbprint hard.
The lighter channels in each grouping show joints that were tooled before being thumbprint hard, bringing excess water and paste to the surface. Joints that are tooled in haste have a weaker surface paste that will come off over time. This could be compared to a concrete finished too quickly, which leaves a weak, thin surface that will pop off, or spall. In addition, joints that are struck in this manner often leave a drag mark from the jointer.
The darker channels were struck after the mortar set slightly too hard. When mortar joints are struck beyond the initial set, there is not enough water present to bring a paste to the joint surface, which results in the joint being slightly porous and dark.
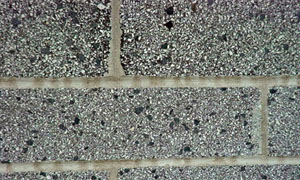
For this reason - and prior to construction - a mock test panel should be erected using the raw materials and masonry units that will be used on the project. It is simply not good enough to pick colors from a pigment company's color kit and expect those colors to match the masonry wall exactly.
If the walls are to be washed, the test panel should also be washed in the same manner as it will in construction. Prior to washing, the wall should be wetted down. If walls are not wetted, the masonry joints will absorb the cleaning agent and result in the etching or "burning" of the joint. In addition to leaving a dark appearance, it can leave the joint porous and subject to moisture penetration. For this reason, use cleaning solutions that are recommended for colored masonry and follow the manufacturer's guidelines.
As seen in the reference channels, the appearance of colored mortar can vary even when materials are measured precisely. After the desired colored mortar is chosen, erect a test panel prior to construction to ensure that the owner, architect and masons are all on the same page prior to construction. As evidenced throughout this article, water demand will vary throughout the course of a project, so always tool mortar joints when mortar has a uniform hardness - when joints are thumbprint hard.
About the Author
Jeff Leonard is vice president of bulk materials for The QUIKRETE Companies, located in Milwaukee, Wisc.