The Chemistry of Waterproofing
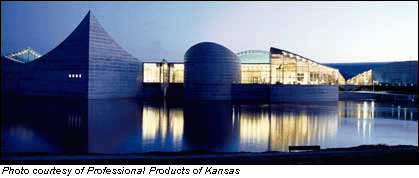
Organic sealants are easily broken down and one should not expect them to provide protection beyond a few years. When it comes to clear, penetrating, breathable water repellants for use on above-grade, porous substrates, you basically have three options: silanes, siloxanes or room temperature vulcanizing (RTV) silicone rubber. All three are similar in that:
- They contain silicone in some form.
- They are penetrants.
- They allow the substrate to breathe, allowing moisture vapor to escape while keeping water out. This is extremely important as it prevents freeze-thaw damage.
- There is little or no change to the appearance of the substrates to which they are applied ? they cure to a clear, flat finish.
Silanes and Siloxanes
The technologies differ in their composition, solids content and capabilities. I mentioned that silane, siloxane and silicone rubber repellants contain some form of silicone. Silanes and siloxanes are produced from the same basic raw material, silane. Being organic, their resistance to ultraviolet rays, salt spray, acid rain and airborne pollutants is somewhat limited. They are easily broken down and one should not expect them to provide protection beyond a few years.
When applied, silane and siloxane repellants penetrate into the substrate and react chemically with the alkalinity therein to form a resin. The resin that forms has no elastomeric properties and is designed to make the capillaries of the substrate smaller than that of a water molecule. This is what provides the repellency. In order for the chemical reaction to take place, which is necessary for forming and bonding of the resin within the substrate, silica must be present. Therefore, unless a catalyst is added in the manufacturing process, silanes and siloxanes are not effective in sealing substrates such as natural stone or wood.
Silanes have the smallest molecular structure and are typically used on your denser surfaces such as horizontal and poured in place, smooth face concrete. Highly volatile, up to 40 percent of the silane material can be lost to evaporation prior to the reactive forming of the resin. Siloxanes have a slightly larger molecular structure and are somewhat effective on substrates up to medium porosity such as heavyweight, smooth-faced, concrete block. Unlike silanes, their chemical composition does not encourage rapid evaporation. Therefore, their solids content is usually less than that of silanes.
"Silanes are the deepest penetrants and they can penetrate fairly deep into the masonry," says Vicky Hall, Sales and Marketing Director for Professional Products of Kansas. "Siloxanes don't penetrate as deep as silanes, but deeper than the silicone rubber."
Neither silanes nor siloxanes, as a result of their molecular structure, are very effective at sealing your more porous substrates such as lightweight, split-face or expanded shale block.
Silicone Rubber
Unlike the silanes and siloxanes, repellants manufactured using room temperature vulcanizing (RTV) silicone rubber react with porous substrates without the requirement for alkali to be present; therefore, they can seal any porous building material including natural stone.
The silicone rubber, used in this class of repellants, has been refined to the point of being inorganic. Ultraviolet rays, acid rain, salt spray or airborne pollutants do not break it down. This provides for long lasting protection.
"It's still working on vertical surfaces, that we know of, that were treated 16 or 17 years ago," says Hall. "To say that it's never going to break down, I can't tell you that. We have data indicating that the raw material (silicone rubber) has been evaluated in actual use, in all climates, showing no deterioration after 30 years.
Additionally, in the cured state, silicone rubber repellants retain the 400% elasticity of the raw material. This enables the bridging of minor structural defects such as hairline cracks, eliminating the need to repoint or caulk every minor flaw.
"In new construction, assuming that the flashing, weeps and damp-proofing are properly installed, it may seem that application of a water repellant is unnecessary, however it should be considered as the final step in completing the building envelope," says Hall. "You're adding one more element of protection and protecting the structure for the long-term."
Strength in Numbers
Professional Products of Kansas, Inc. manufactures an RTV silicone rubber sealant (Professional? Water Sealant) that is available in three strengths which compensate for varying porosities of building materials. These products can effectively seal even the most porous substrates with only one coat provided that the strength appropriate to the porosity of the substrate is used.
"One application will provide protection for over ten years," adds Hall. "That's what we guarantee."
Graffiti Protection
Professional Water Sealant is also used as an effective, non-sacrificial barrier against graffiti. Unlike waterproofing, graffiti protection requires a two-coat application.
Once the sealant has been applied it allows for the easy removal of graffiti. Treated surfaces can withstand repeated cycles of tagging and removal with no requirement to reapply the sealant.
About the Author
Ken Barry is active in the construction industry. He has been involved with associations such as: National Paint and Coatings Association, Construction Specifications Institute, American Institute of Architects, Brick Institute of America, International Parking Institute and the Sealant, Waterproofing and Restoration Institute. He is also an active speaker and presenter throughout the country.