June 9, 2009 7:39 AM CDT
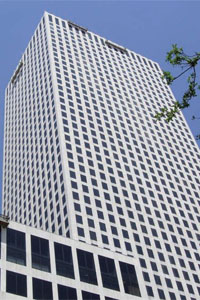
If there is anything typical in restoration, it is perhaps that nothing is typical. Things rarely turn out to be as they first appear. This challenge is both exciting and satisfying when the project is complete. This is certainly true in the case of One Shell Square, in New Orleans.
One Shell Square was built in 1972 and was, for several years, the tallest structure in Louisiana. The building is a 52-story, double tube system, with a steel core and concrete perimeter. The exterior cladding is in Italian travertine with bronze insulated glass units set in a structural gasket. It was the first southern skyscraper to reach 200 meters in height, and has a total square footage of about 1,732,000 square feet. The restoration project started life in 2004 as a Panel Stabilization/Caulking job, but after Hurricane Katrina in August of 2005, it became a catastrophic, multi-disciplined restoration endeavour.
As is correct procedure, the consultant first tested and verified the suitability of using the most economical solution for panel stabilization, helical wall ties. Travetine from the building was shipped up to the consultant’s office in Dallas, Texas, and tests were conducted to establish the optimal tie diameter and drilling technique to maximize the pull-out capacity of the tie in the stone.
Helical wall ties are the most cost-effective way of retrofitting a connection between the veneer and the structural back-up of a building. The system entails pre-drilling a pilot hole though both components of the wall. Then, using the hammer action of an SDS hammer drill through a special installation tool, the helical tie is driven into place down the pilot hole to make a threaded connection, rather like a self-tapping screw, between the two wall components. No torque is applied during this operation, and the possibility of over-torquing and stripping the thread is, therefore, eliminated. Since the size and form of the tie and the material itself are a given, the only variable is the pilot hole diameter. Varying the pilot hole diameter to optimize the tie pull-out capacity is really the issue when conducting such testing. As a rule of thumb, the softer the material, the smaller the pilot hole required. This, like most engineering, is just common sense. Hard material is more difficult to cut, and the helical tie has the propensity to “ground out,” rather than cut a thread form through the material. Similarly, a softer material needs more bearing surface on the thread form to achieve an equivalent pull-out load bearing capacity.
The travertine stone from One Shell Square is considered a relatively soft material, and because of its inherent pourosity and hidden fissures, a 10-mm diameter helical tie was found to consistently produce the best results. After a series of tests in both wet and dry stone, an installation protocol was established for the travertine, which consistently achieved a pull-out load bearing capacity of between 900 and 950 lbf. Setting helical ties in poured concrete almost always generates a pull-out strength in excess of 1,000 lbf, so an ultimate connection strength of 900 lbf, with the travertine being the weakest link, was established as the design parameter. The die was cast, the specification written, and the job was bid.
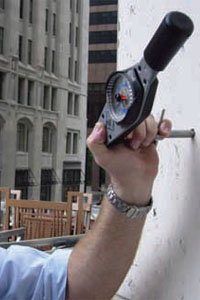
After the contract was awarded, mock-ups were performed on the building. Unknown to all parties at the time of undertaking the initial series of tests, poured concrete in Louisianna, is the hardest concrete to be found anywhere in North America. A little puff of white dust while setting the helical tie through the travetine and into the poured concrete could easily have been overlooked. But that tell-tail puff of white dust evidenced the destruction of the thread form in the travertine as the the tie vibrated while being set in the hard concrete backup. This required further investigation.
A travertine panel was removed from the building and mounted on 2 X4 boards, so that once a helical tie had been fullly installed, the tie could be cut, the stone removed, and a load test conducted. That little puff of white powder translated into a reduction of the pull-out capacity of the travertine from 900 lbf to 400 lbf. If a safety factor of four is applied, then the design strength of the connection between the stone and the concrete back-up became 100lbf, which on a 52-story building in a hurricane zone, is a little too close for comfort. Clearly, another solution was necessary, one which would not have a hugely negative impact cost-wise, since the contract had already been awarded based on the original design.
A torque-activated mechanical anchor was modified to enable it to expand within the body of the 30-mm thick travertine stone, while enabling it sufficiently below the surface of the stone to enable a patch to be applied to complete the repair. A series of tests was conducted with this anchor in both the travertine and the poured concrete back-up. The results showed a pull-out capacity in the travertine of about 1,500 lbf, and in excess of 2,500 lbf in the concrete back-up. Work then commenced installing this new anchor system. Only two lengths of anchor were used on the whole building with any variance in the cavity between the stone veneer and the structural back-up be accommodated by over-drilling into the concrete and setting the anchor deeper. Bore-scope analysis showed positive engagement of the anchors in both the travertine and concrete back-up.
Hurricane Katrina swept through New Orleans in August 2005 and quadrupled the scope of work as the protocol changed to ensure that all veneer panels that appeared loose were anchored as an emergency repair. Due to the instability of the travertine panels and the glass, the entire building had to be roof rigged. This entailed the utilization of a custom engineered and installed tower scaffolding system in order to make all stage moves from the top of the building. Naturally, the additional cost of this work caught the attention of the insurance companies, and they brought in their peer review engineers to review the work being done. The anchor system passed with flying colors.
In addition, all of the travertine panels had to be removed from the tower penthouse due to storm damage. A new engineered system was developed and 1,128 pieces of new stone were installed and secured using a mechanical torque activated anchor in the CMU back-up. The panel itself was sandwiched between a recessed wide flanged nut, and a stainless steel toggle on the back of the stone. This effectively transferred both tensile and compressive live wind loads through the anchor into the structural back-up. This will also ensure that the stone panels will remain secure during future hurricanes, and that means peace of mind.
The consultant for the project was Stone & Glazing Consulting, the restoration contractor was American Restoration Inc, and the anchor systems were supplied by Blok-Lok Limited, a Hohmann & Barnard company.
Rehab and Restoration: Adjusting Accordingly
There is nothing is typical in restoration
By Masonry
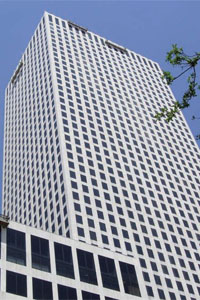
One Shell Square was built in 1972 and for several years was the tallest structure in Louisiana.
One Shell Square was built in 1972 and was, for several years, the tallest structure in Louisiana. The building is a 52-story, double tube system, with a steel core and concrete perimeter. The exterior cladding is in Italian travertine with bronze insulated glass units set in a structural gasket. It was the first southern skyscraper to reach 200 meters in height, and has a total square footage of about 1,732,000 square feet. The restoration project started life in 2004 as a Panel Stabilization/Caulking job, but after Hurricane Katrina in August of 2005, it became a catastrophic, multi-disciplined restoration endeavour.
As is correct procedure, the consultant first tested and verified the suitability of using the most economical solution for panel stabilization, helical wall ties. Travetine from the building was shipped up to the consultant’s office in Dallas, Texas, and tests were conducted to establish the optimal tie diameter and drilling technique to maximize the pull-out capacity of the tie in the stone.
Helical wall ties are the most cost-effective way of retrofitting a connection between the veneer and the structural back-up of a building. The system entails pre-drilling a pilot hole though both components of the wall. Then, using the hammer action of an SDS hammer drill through a special installation tool, the helical tie is driven into place down the pilot hole to make a threaded connection, rather like a self-tapping screw, between the two wall components. No torque is applied during this operation, and the possibility of over-torquing and stripping the thread is, therefore, eliminated. Since the size and form of the tie and the material itself are a given, the only variable is the pilot hole diameter. Varying the pilot hole diameter to optimize the tie pull-out capacity is really the issue when conducting such testing. As a rule of thumb, the softer the material, the smaller the pilot hole required. This, like most engineering, is just common sense. Hard material is more difficult to cut, and the helical tie has the propensity to “ground out,” rather than cut a thread form through the material. Similarly, a softer material needs more bearing surface on the thread form to achieve an equivalent pull-out load bearing capacity.
The travertine stone from One Shell Square is considered a relatively soft material, and because of its inherent pourosity and hidden fissures, a 10-mm diameter helical tie was found to consistently produce the best results. After a series of tests in both wet and dry stone, an installation protocol was established for the travertine, which consistently achieved a pull-out load bearing capacity of between 900 and 950 lbf. Setting helical ties in poured concrete almost always generates a pull-out strength in excess of 1,000 lbf, so an ultimate connection strength of 900 lbf, with the travertine being the weakest link, was established as the design parameter. The die was cast, the specification written, and the job was bid.
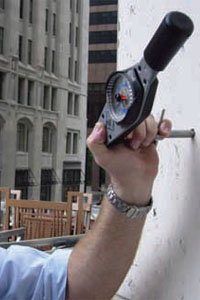
Testing the torque. Image courtesy of Hohmann and Barnard.
A travertine panel was removed from the building and mounted on 2 X4 boards, so that once a helical tie had been fullly installed, the tie could be cut, the stone removed, and a load test conducted. That little puff of white powder translated into a reduction of the pull-out capacity of the travertine from 900 lbf to 400 lbf. If a safety factor of four is applied, then the design strength of the connection between the stone and the concrete back-up became 100lbf, which on a 52-story building in a hurricane zone, is a little too close for comfort. Clearly, another solution was necessary, one which would not have a hugely negative impact cost-wise, since the contract had already been awarded based on the original design.
A torque-activated mechanical anchor was modified to enable it to expand within the body of the 30-mm thick travertine stone, while enabling it sufficiently below the surface of the stone to enable a patch to be applied to complete the repair. A series of tests was conducted with this anchor in both the travertine and the poured concrete back-up. The results showed a pull-out capacity in the travertine of about 1,500 lbf, and in excess of 2,500 lbf in the concrete back-up. Work then commenced installing this new anchor system. Only two lengths of anchor were used on the whole building with any variance in the cavity between the stone veneer and the structural back-up be accommodated by over-drilling into the concrete and setting the anchor deeper. Bore-scope analysis showed positive engagement of the anchors in both the travertine and concrete back-up.
Hurricane Katrina swept through New Orleans in August 2005 and quadrupled the scope of work as the protocol changed to ensure that all veneer panels that appeared loose were anchored as an emergency repair. Due to the instability of the travertine panels and the glass, the entire building had to be roof rigged. This entailed the utilization of a custom engineered and installed tower scaffolding system in order to make all stage moves from the top of the building. Naturally, the additional cost of this work caught the attention of the insurance companies, and they brought in their peer review engineers to review the work being done. The anchor system passed with flying colors.
In addition, all of the travertine panels had to be removed from the tower penthouse due to storm damage. A new engineered system was developed and 1,128 pieces of new stone were installed and secured using a mechanical torque activated anchor in the CMU back-up. The panel itself was sandwiched between a recessed wide flanged nut, and a stainless steel toggle on the back of the stone. This effectively transferred both tensile and compressive live wind loads through the anchor into the structural back-up. This will also ensure that the stone panels will remain secure during future hurricanes, and that means peace of mind.
The consultant for the project was Stone & Glazing Consulting, the restoration contractor was American Restoration Inc, and the anchor systems were supplied by Blok-Lok Limited, a Hohmann & Barnard company.
About the Author
Masonry, the official publication of the Mason Contractors Association of America, covers every aspect of the mason contractor profession - equipment and techniques, building codes and standards, business planning, promoting your business, legal issues and more. Read or subscribe to Masonry magazine at www.masonrymagazine.com.