November 9, 2009 8:04 AM CST
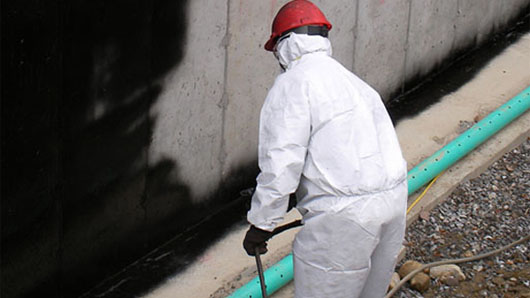
With moisture-related problems in both new construction and older buildings equally prevalent in the news, there is no doubt that air and vapor barriers should be a well used and understood tool in a designer’s bag of tricks. However, depending on a number of factors – such as the climate of the given location, the building materials used in the project, building codes, and other key design issues – the type of barrier and the appropriate location within the system’s structure vary greatly.
It was once thought that water vapor through diffusion was the culprit in potential moisture problems in building design; however, experts discovered that air leakage provided a far greater ability to carry more moisture through miniscule holes, seams and other penetrations. Surprisingly, air leakage is capable of depositing several gallons of moisture each year into the system, 30 to 40 times greater than by diffusion. The use of an effective air-vapor barrier system can limit this moisture penetration through the CMU backup or sheathing and help eliminate the potential damage.
“Quite honestly, there are a lot of areas of the country where people aren’t nearly as familiar with air-vapor barriers and their installation as you might think,” says Christopher Bupp, technical services for Hohmann and Barnard, Inc.
While vapor and air barriers can be considered moisture barriers, the opposite is not the case.
The IECC requires vapor barriers to be used in colder climates, with a few exceptions; the International Building Code (IBC), by referencing the IECC, therefore also has the same requirement.
While air barriers can be vapor permeable or vapor impermeable, there are several requirements of the air barrier system that must be met. An air barrier system must be able to resist live loads (e.g., wind pressure, HVAC mechanical loads, etc.) without failing, and the system must completely wrap the entire building envelope completely, without presenting any entry points for air leakage. Each air barrier component, assembly and the connections between them must be connected, from the roofing system to the below-grade structure, to resist these loads. A failure of any part of the system is a failure of the system as a whole.
While the 2006 IBC does not require an air barrier in exterior wall systems, experts suggest that we should expect a mandatory air barrier requirement with the 2009 IBC. Several factors play a part in this expectation.
First, the well received National Building Code of Canada requirements specify the acceptable level of air permeability of 0.02 L/(s-m2) at 75 Pa pressure (0.004 cfm/ft2 at 1.57 psf); several states and municipalities in the United States have adopted this requirement as well.
Second – and more importantly – AHRAE 90.1 “Energy Standard for Buildings Except Low-Rise Residential Buildings” was updated in 2006 requiring the use of air barriers, which is adopted by reference by the IECC, which once again will be adopted by reference by the IBC in 2009.
Briefly, key design considerations in specifying the appropriate product include:
If there is any doubt as to the appropriate material to choose for a particular project, your air barrier manufacturer can assist you in specifying the correct product.
The U.S. Department of Energy determined that 40 percent of the energy consumed to heat or cool a building is due to air leakage. However, according to a 2006 National Institute of Standards and Technology study, a properly specified and installed air barrier system can provide an energy cost savings of approximately 32 to 39 percent, with the largest savings going to buildings in colder climates. Also, due to this significant energy efficiency capability, air barriers can provide points toward a building’s LEED certification.
In addition, air barrier products themselves are getting greener, such as Hohmann and Barnard’s TextroFlash™ Green, a multi-purpose, flexible, self-adhered membrane manufactured from 45 percent recycled content, and TextroFlash™ Liquid, a VOC- and HAPs-free liquid air-vapor barrier.
While each type of air barrier product will have its own installation procedure, there are a number of steps that should be considered in masonry construction, regardless of the product.
Understanding Air and Vapor Barriers
A necessary tool to comprehend
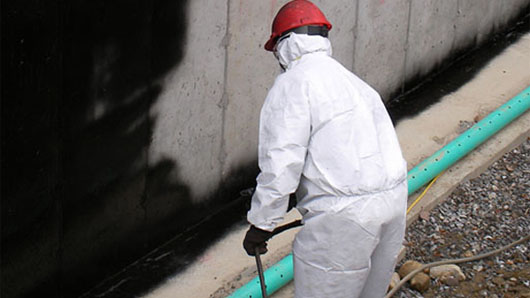
The successful inclusion of an air barrier system in building projects can be a rewarding experience for the designer and owner.
With moisture-related problems in both new construction and older buildings equally prevalent in the news, there is no doubt that air and vapor barriers should be a well used and understood tool in a designer’s bag of tricks. However, depending on a number of factors – such as the climate of the given location, the building materials used in the project, building codes, and other key design issues – the type of barrier and the appropriate location within the system’s structure vary greatly.
Moisture Movement in the Built Environment
Moisture can present itself in the built environment in a number of ways. The main avenues for water infiltration are:- Kinetic energy – Rainwater driven through the roof system, mortar joints or other entry point
- Capillary action – Water seepage through cracks, holes or drawn toward drier environments
- Gravity – Water flow down sloping design elements with entry into the building envelope
- Pressure differential – Pressure differences in the building envelope that push the water into openings
- Water vapor – Moisture transported by diffusion or air leakage.
It was once thought that water vapor through diffusion was the culprit in potential moisture problems in building design; however, experts discovered that air leakage provided a far greater ability to carry more moisture through miniscule holes, seams and other penetrations. Surprisingly, air leakage is capable of depositing several gallons of moisture each year into the system, 30 to 40 times greater than by diffusion. The use of an effective air-vapor barrier system can limit this moisture penetration through the CMU backup or sheathing and help eliminate the potential damage.
Differences Between Air, Vapor and Moisture Barriers
With close similarities between air, vapor and moisture barriers – as well as the fact that certain products or systems can be considered to be more than one type of barrier – confusion is bound to occur.“Quite honestly, there are a lot of areas of the country where people aren’t nearly as familiar with air-vapor barriers and their installation as you might think,” says Christopher Bupp, technical services for Hohmann and Barnard, Inc.
Moisture Barriers
Moisture – or weather-resistive – barriers are intended to prevent non-vapor, liquid water from infiltrating the wall system. The International Building Code (IBC) requires moisture barriers to be integrated into the moisture management system for most types of wall designs. This system is effective in deflecting liquid, but – once again – provides no protection against vapor diffusion or air leakage.While vapor and air barriers can be considered moisture barriers, the opposite is not the case.
Vapor Barriers
According to the International Energy Conservation Code (IECC), a vapor barrier is: “A vapor-resistant material, membrane or covering such as foil, plastic sheeting, or insulation facing having permeance rating of one perm (5.7 X 10-11 kg/PA.s.m2) or less when tested in accordance with the desiccant method using Procedure A of ASTM E 96.” The vapor barrier is effective in limiting moisture infiltration by means of diffusion, but typically not designed to effectively limit air leakage and the moisture accompanying it.The IECC requires vapor barriers to be used in colder climates, with a few exceptions; the International Building Code (IBC), by referencing the IECC, therefore also has the same requirement.
Air Barriers
By contrast, an air barrier is any material that restricts the flow of air under pressure through a building envelope. According to the Air Barrier Association of America, the air permeance of any air barrier material is 0.02L(s•m2) at 75Pa. While many materials singularly can achieve this air permeance, the air barrier materials must be tied together in a continuous plane to form an assembly, with a maximum air leakage of 0.2 L(s•m2) at 75 Pa. Finally, the actual air barrier system consists of these air barrier assemblies in a continuous plane of air tightness for the entire building enclosure, with a maximum air leakage of the whole building at 2.0 L(s•m2) at 75 Pa.While air barriers can be vapor permeable or vapor impermeable, there are several requirements of the air barrier system that must be met. An air barrier system must be able to resist live loads (e.g., wind pressure, HVAC mechanical loads, etc.) without failing, and the system must completely wrap the entire building envelope completely, without presenting any entry points for air leakage. Each air barrier component, assembly and the connections between them must be connected, from the roofing system to the below-grade structure, to resist these loads. A failure of any part of the system is a failure of the system as a whole.
While the 2006 IBC does not require an air barrier in exterior wall systems, experts suggest that we should expect a mandatory air barrier requirement with the 2009 IBC. Several factors play a part in this expectation.
First, the well received National Building Code of Canada requirements specify the acceptable level of air permeability of 0.02 L/(s-m2) at 75 Pa pressure (0.004 cfm/ft2 at 1.57 psf); several states and municipalities in the United States have adopted this requirement as well.
Second – and more importantly – AHRAE 90.1 “Energy Standard for Buildings Except Low-Rise Residential Buildings” was updated in 2006 requiring the use of air barriers, which is adopted by reference by the IECC, which once again will be adopted by reference by the IBC in 2009.
Types of Air Barriers
There are several different types of air barrier materials available:- Mechanically-attached membranes, also commonly referred to as housewraps, that allow vapor transmission
- Self-adhered membranes, aka peel and stick, which are typically waterproof and vapor impermeable
- Fluid-applied membranes, such as heavy-bodied paints or coatings
- Closed-cell spray-applied polyurethane foam, which typically provides insulation as well
- Thermofusible materials, typically made with SBS-modified asphalt that is “melted” to the substrate.
Briefly, key design considerations in specifying the appropriate product include:
- The type of construction materials being used (e.g., brick cladding and CMU backup)
- Overall climate for the given location and temperature during installation
- Compatibility of the materials being used
- Timeframe for construction completion
- Product durability
- Efficient application
- Code compliance.
If there is any doubt as to the appropriate material to choose for a particular project, your air barrier manufacturer can assist you in specifying the correct product.
Going Green
Not only do air barriers make sense in creating a healthier environment by limiting the potential for moisture-related problems, but they are also a great addition to a building’s overall sustainable design. Masonry buildings already provide significant energy and lifecycle savings, but air barriers are an additional improvement to both of these areas for owners and occupants.The U.S. Department of Energy determined that 40 percent of the energy consumed to heat or cool a building is due to air leakage. However, according to a 2006 National Institute of Standards and Technology study, a properly specified and installed air barrier system can provide an energy cost savings of approximately 32 to 39 percent, with the largest savings going to buildings in colder climates. Also, due to this significant energy efficiency capability, air barriers can provide points toward a building’s LEED certification.
In addition, air barrier products themselves are getting greener, such as Hohmann and Barnard’s TextroFlash™ Green, a multi-purpose, flexible, self-adhered membrane manufactured from 45 percent recycled content, and TextroFlash™ Liquid, a VOC- and HAPs-free liquid air-vapor barrier.
Basic Installation Steps
Just as well researched and exact designs and specifications are important to the successful implementation of an air barrier system for any given project, installation is equally important for the overall satisfactory completion.While each type of air barrier product will have its own installation procedure, there are a number of steps that should be considered in masonry construction, regardless of the product.
- Specify flush masonry joints for the CMU backup, with joints completely filled
- Any excess mortar on the substrate and ties should be removed
- Mortar should reach the minimum cure period recommended by the air barrier manufacturer prior to installation
- Complete a full examination of the CMU backup substrate prior to installation, verifying it is clean and free of moisture
- Consider the weather conditions under which the air barrier assemblies will be applied and make changes accordingly
- Ensure any work by other trades that may penetrate through the air barrier system is in place and complete
- Prime the CMU backup according to manufacturer’s recommendations
- Seal vertical and horizontal surfaces at terminations and penetrations
- Connect air barrier assemblies in exterior wall continuously to the air barrier of the roof, to below-grade structures, to windows, curtain wall, storefront, louvers, exterior doors and other intersection conditions and perform sealing of penetrations, using accessory materials and in accordance with the manufacturer’s recommendations.
- Plan accordingly for changes in substrate plane, through-wall flashings, control and seismic joints, and any other gaps to ensure continuous transitions
- During the installation and construction process, the membrane should receive appropriate protection at the end of each work day
- Do not allow materials to come in contact with chemically incompatible materials
- Do not expose membrane to sunlight longer than recommended by the manufacturer
- Always install materials in accordance with manufacturer’s recommendations
- Prior to enclosing the assembly, inspect and repair any damaged areas of the air barrier system.
Conclusion
The successful inclusion of an air barrier system in building projects can be a rewarding experience for the designer and owner. Whether the project is commercial or residential – even a multi-tenant building – can reap benefits from the healthy environment, reduction in energy consumption, and increased building valuation.About the Author
Jennie Farnsworth is an Atlanta-based freelance writer and editor. She is a former editor of Masonry magazine.